I am lucky enough to have CAD software and was able to create a 3d surfaced model in the computer of what I wanted and from there get all the dimensions needed. This of course is not necessary as it could be drawn on paper manually.
I decided to use black foam board and knowing all the sizes and shapes needed was able to draw them all on the foam board prior to cutting to get the least amount of waste.
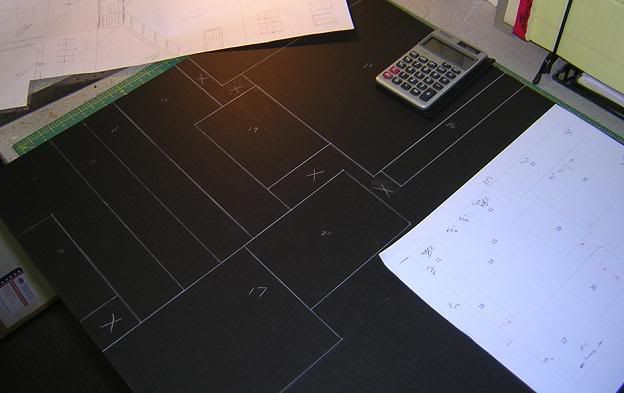
After cutting out for the windows and doors, I used hot wax to glue the walls together.
Do not glue the windows and doors until after the veneer siding is installed.
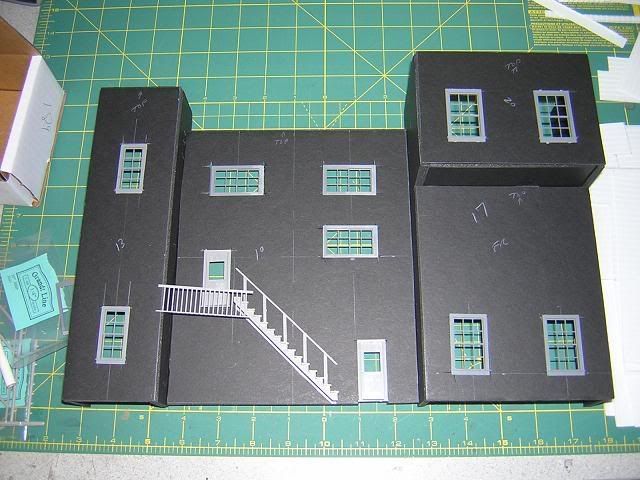
To strengthen the assembly I used wood glued to the walls with yellow glue.
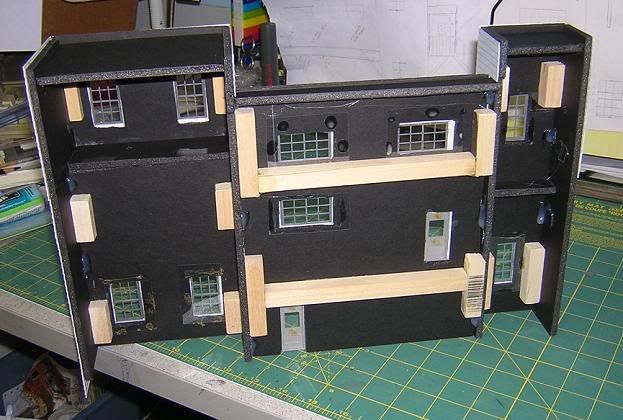
Test fitted the structure in place after building a base to hold it.
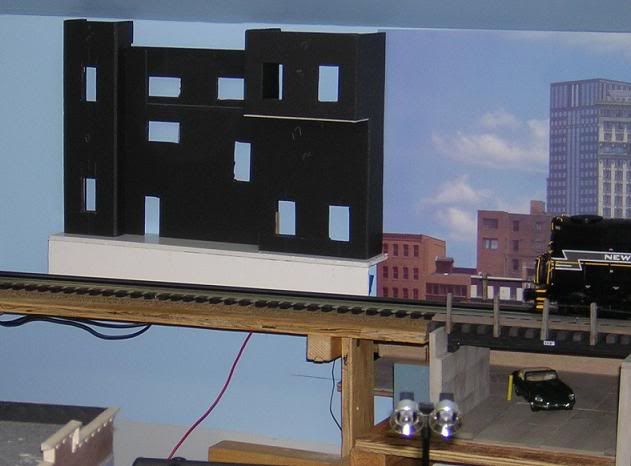
Siding (plastic from Precision Products) was cut to size and installed
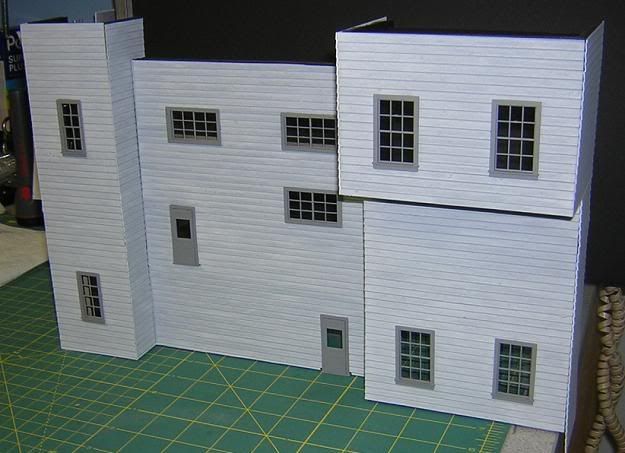
Finished unit with details, lights and secured to wall.
I decided to name it Bassette Printing Co. in honor of that fine family.
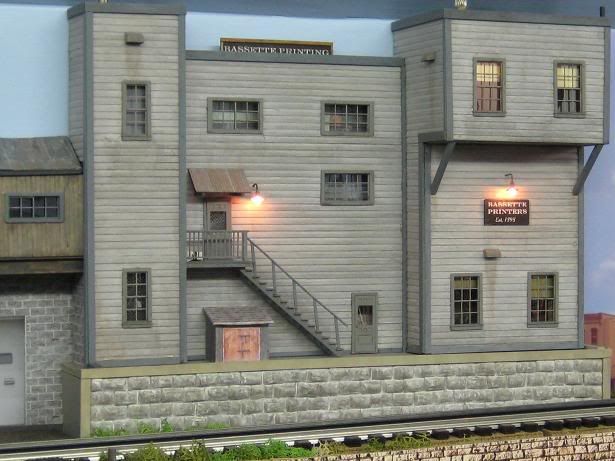